Planet
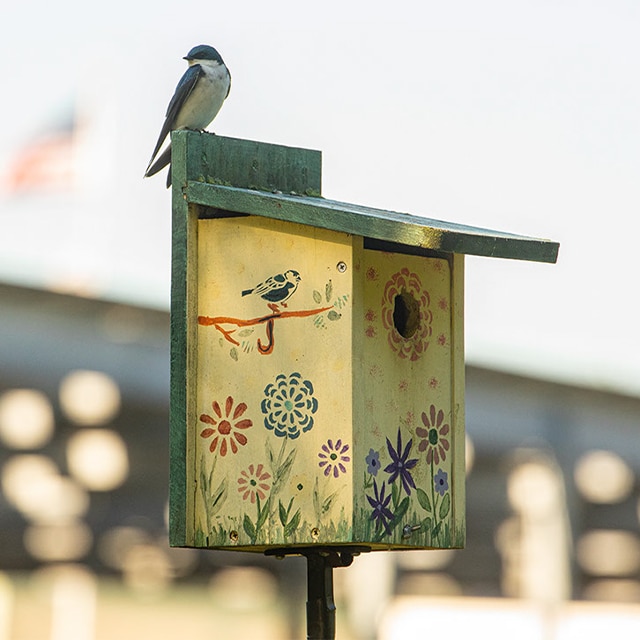
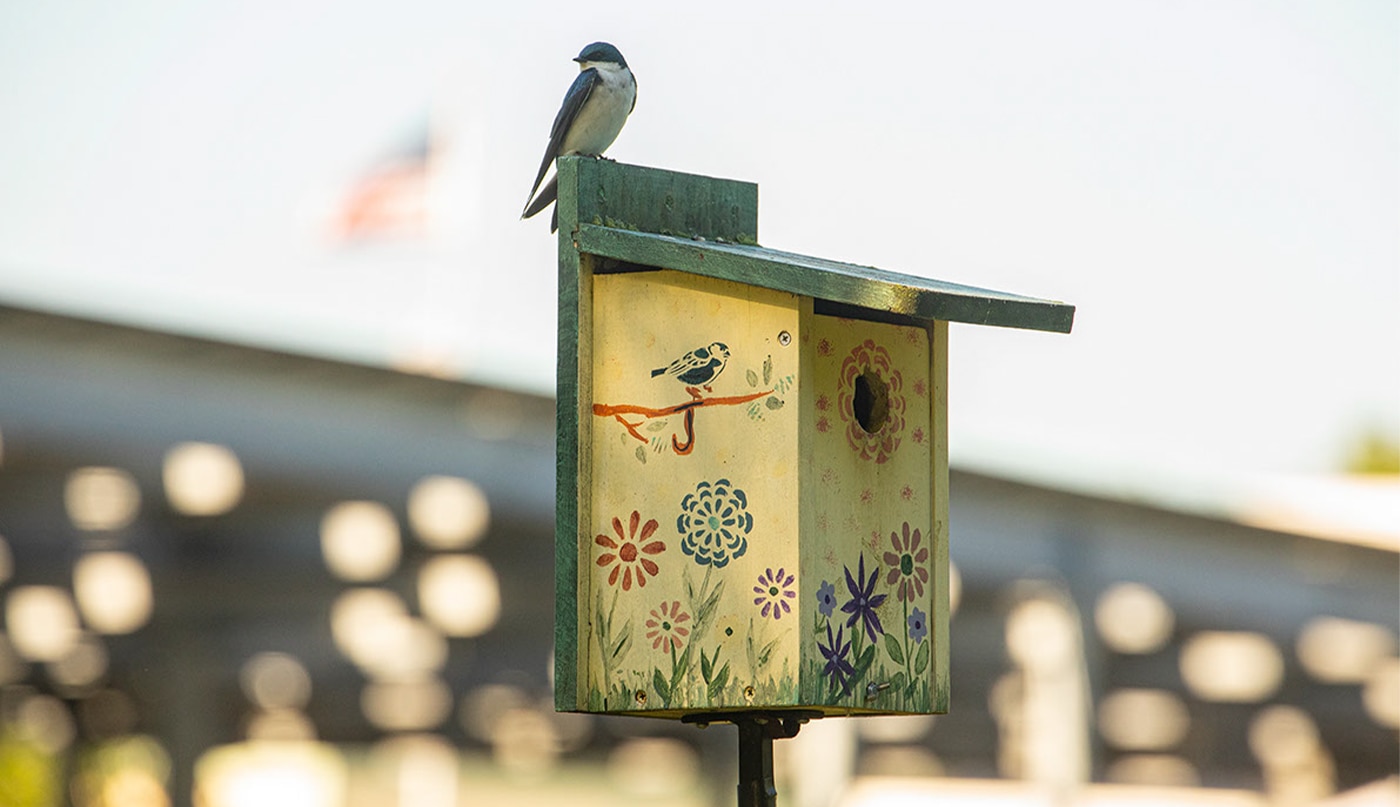
Environmental Management
Assuring compliance with applicable environmental, health, safety, security (EHSS), and product safety laws and regulations is inherent in the company’s operating management. It is a critical piece of our commitment to sustain the quality of our planet for future generations.
Benjamin Moore has a robust EHSS management system and internal policies and procedures that enable us to prevent and detect noncompliance with state, federal, and local regulations. We actively strive to reduce the adverse impacts of our activities, products, and services on the environment.
Our cross-functional EHSS leadership team consists of corporate, manufacturing, and distribution representatives who focus on and drive our positive safety culture. This group oversees compliance, performance, and EHSS topics affecting Benjamin Moore. It is responsible for overall governance, setting standards and priorities aligned with the business goals, and driving consistency between functional areas.
WASTE MANAGEMENT
Benjamin Moore is continually exploring new ways to reduce waste. Wash water minimizes the amount of water needed in the manufacturing process. In 2024, we redirected almost 2.8 million gallons of wash water and wash solvent into low-grade products, keeping it out of the waste stream. Additionally, we recycled more than 550,000 gallons of paint that would otherwise become waste.
Our distribution centers ship hundreds of thousands of gallons of paint per day. We have implemented many recycling programs to help decrease waste, including recycling systems for wooden pallets, corrugated cardboard, shrink wrap, and tin cans.
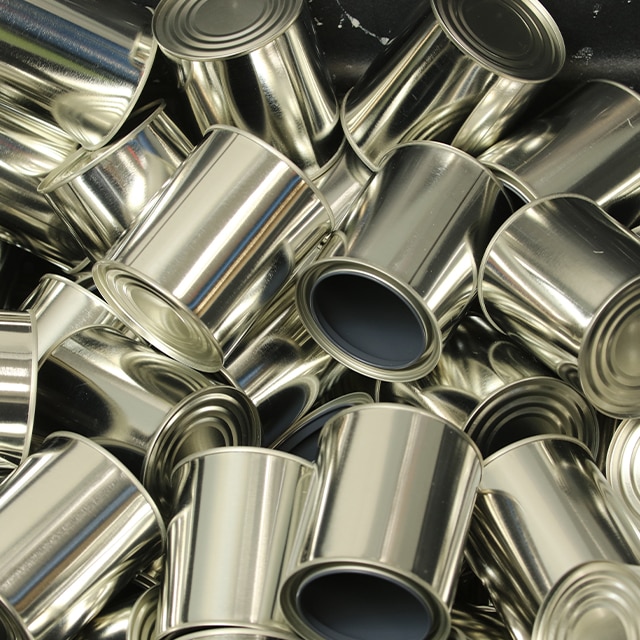
PaintCare®
We regularly seek new ways to improve the management of unused paint. Benjamin Moore partners with the American Coatings Association (ACA) and the Canadian Paint and Coatings Association (CPCA).
The ACA’s nonprofit entity, PaintCare, operates in states with paint stewardship laws and manages an industry-wide program to collect leftover paint for reuse, recycling or safe disposal. Product Care oversees product stewardship programs for household hazardous and special waste products on behalf of its members across Canada. We are a contributing board member for both organizations, and our shared goal is to expand the breadth of these models so post-consumer paint is handled effectively and in an environmentally responsible manner.
Learn more about how to dispose of unused paint properly.
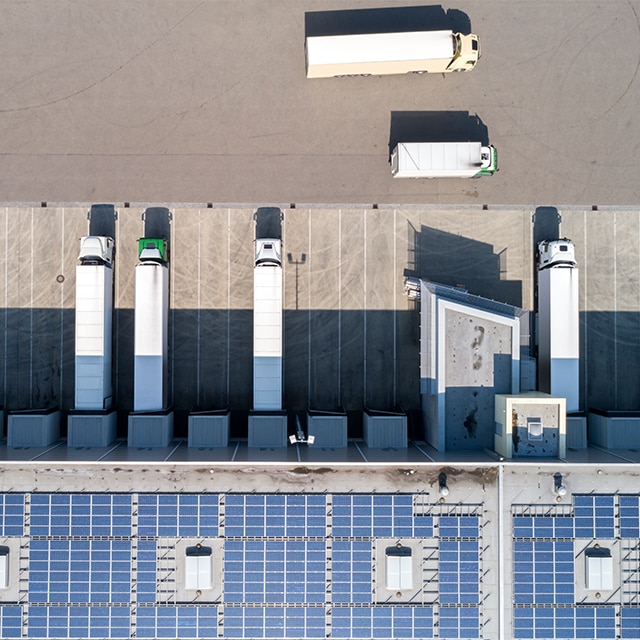
ENERGY CONSERVATION
Several of our facilities employ a solar field to offset electric usage within the facility, and many of our locations have been converted to LED lighting to further reduce energy consumption. We continue to explore additional opportunities to use less energy at our facilities as an ongoing review of our operations.
WILDLIFE PRESERVATION
Our research and development center in Flanders, NJ, and our manufacturing facility and distribution center in Pell City, AL, have earned a Conservation Certification® from the Wildlife Habitat Council® (WHC), a nonprofit group dedicated to restoring and enhancing wildlife habitat. Employee volunteers at these locations manage 67 acres, providing habitat for native birds and pollinators and removing invasive species. Benjamin Moore has participated in this program since 1996.
At our manufacturing location in Pell City, the Fishing Creek Wetlands Habitat serves as an outdoor classroom for middle and high school students receiving a formal conservation education focused on topics linked to curriculum and state STEM requirements. Themes include water quality monitoring, wetlands species identification and inventory, planting, and native food sources.
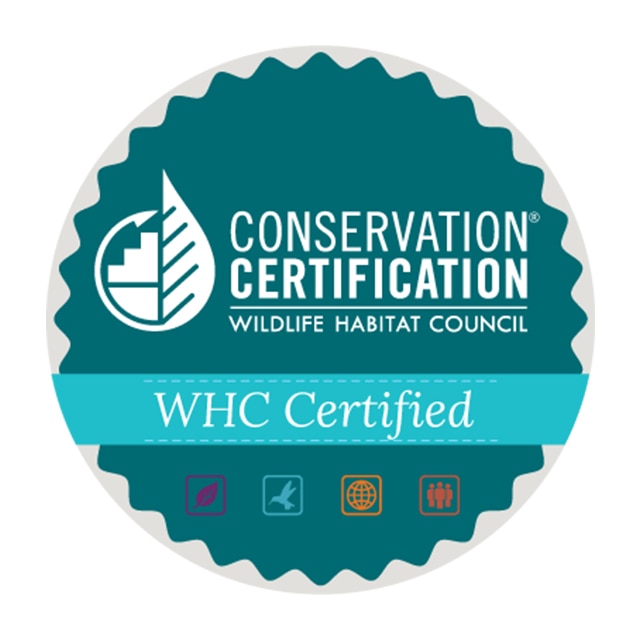
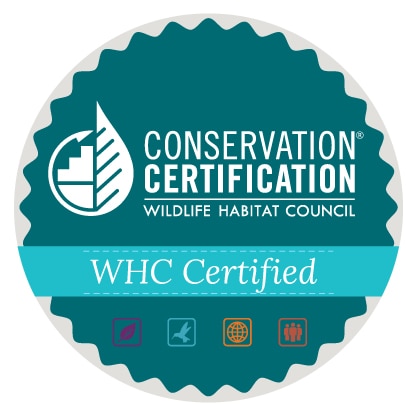
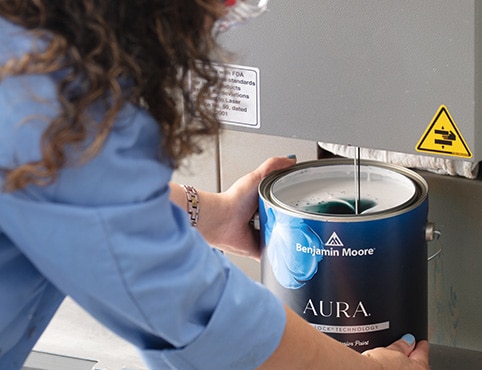
Product
We are committed to delivering products to our customers that are innovative, effective, safe, and minimize our impact on the environment.
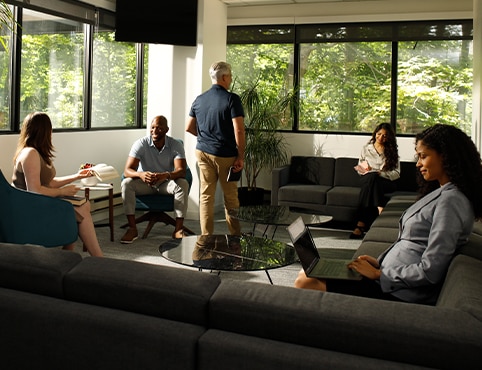
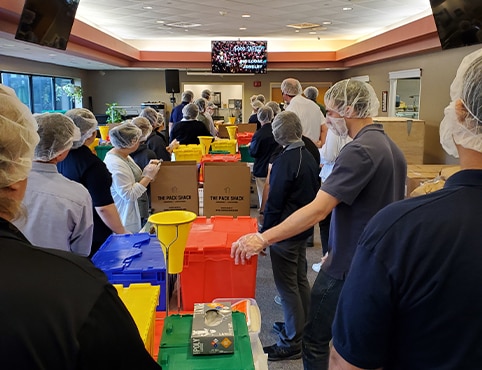
Partnerships
Our goal is to uplift the communities we serve through programs and partnerships that help create healthy, accessible, safe, and inclusive environments.
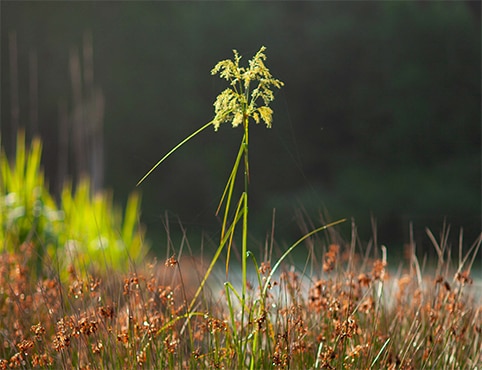
Corporate Responsibility Overview Archive
Reports from previous years are available for download.